Back Legs
Grain direction is very important in curved parts. We select the part so that the grain follows the curves as much as possible in the areas subject to the most load.
When laying out the job, we draw around the back leg pattern on a board and in a position that pass the required tests for structure and appearance. We saw outside the drawn line to rough cut the leg on the bandsaw.
After being planed flat and true to thickness, the leg is clamped in a carriage and cut to accurate line on the pattern shaper. A true line on the carriage is held against a bearing to control the cut. We built this shaper with two cutting heads, one rotates clockwise, the other counterclockwise.
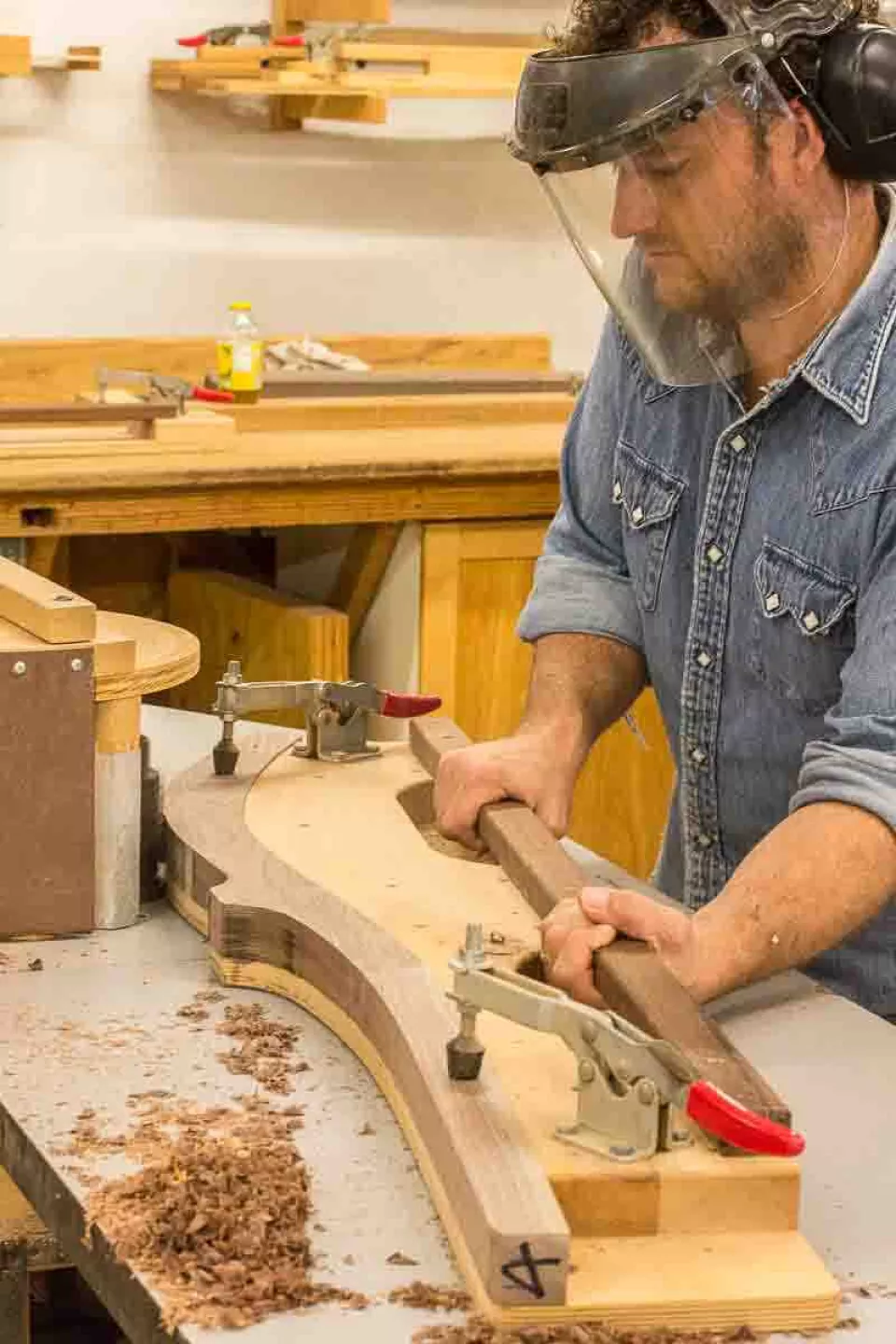
The arm of the rocking chair appears to grow out of the back leg — a treatment called "fairing". Because we cut its mortise and tenon joint snugly, we can drive the arm into the back leg and do much of the fairing on the head of the edge sander. We built this sander to specifically serve our purposes.