Wood chairs scratch wood floors, and other hard surface floors. Our lightweight and tightly constructed chairs make an irritating noise if friction with the floor introduces vibration. An elegant and satisfactory solution for these two problems has been elusive.
There are many varieties of glides and pads offered for sale. These are their general characteristics: Chair glides are made of low-friction plastic. Chair pads are made of felt or carpet. Glides and pads have two basic means of attachment: peel-and-stick adhesive and mechanical fasteners.
Glides (think Teflon) slide well across the floor and reduce the noise of dragging chairs. When new, glides will not mark floors, but when use embeds grit into them . . . scratches happen. Pads, as long as they are in place and sound, reduce vibration and do not mark floors directly or indirectly.
Peel-and-stick adhesives are surprisingly good, but if a glide or pad is stuck directly to the bottom of a chair leg, the side loading inherent in moving the chairs tends to, and will, squish it off to a side, making it first ugly and then ineffective. Fasteners do resist side loading and other detaching forces. Most glides are directly attached by a screw, nail, or other driven fastener. Pads and some glides are stuck into a mechanically fastened cup. Failures do occur — fasteners break or wallow out the wood that holds them. Broken or loose metal fasteners make deep and nasty gouges in floors.
We have tested many glides and pads. Many. We have talked to many manufacturers, retailers, and representatives. In the process and finally, we found the material, designed the attachment, and built the equipment to “pad” our dining chairs, barstools, footstools, and side tables and, therefore, protect the floors they are used on.
We use a US made, woven not compressed, synthetic felt. This felt is thicker and tougher than that found in hardware stores or websearches. This felt comes to us with the highest quality, pressure sensitive adhesive on one side. We stick the felt into a shallow recess in the bottom of our furniture legs, to produce the benefits of a mechanically fastened cup. This recess resists the side loading that moves most felt pads off chair legs.
Developing a way to make these recesses consistent, accurate, level with one another, and hassle-free was very difficult and time-consuming. Hand boring was inconsistent, inaccurate, out of level, and hassle-bound. We have long used the crosscut table top to be sure the chair legs all met the floor and were level to it. I mounted a plunge router under this tabletop, built a mechanism to plunge it and found that we could not hold the chair leg against the force of 22,000RPM’s . . . I lost three days work. I built a contraption to bore the recess with a forstner bit turning less than 1000RPM’s, again mounted under the tabletop of the crosscut saw . . . six days work. Works great.
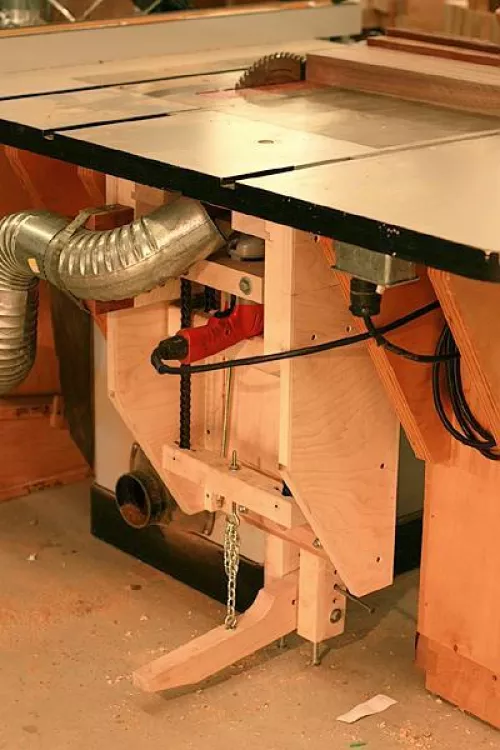
We do the final leveling of the legs on a sanding board.
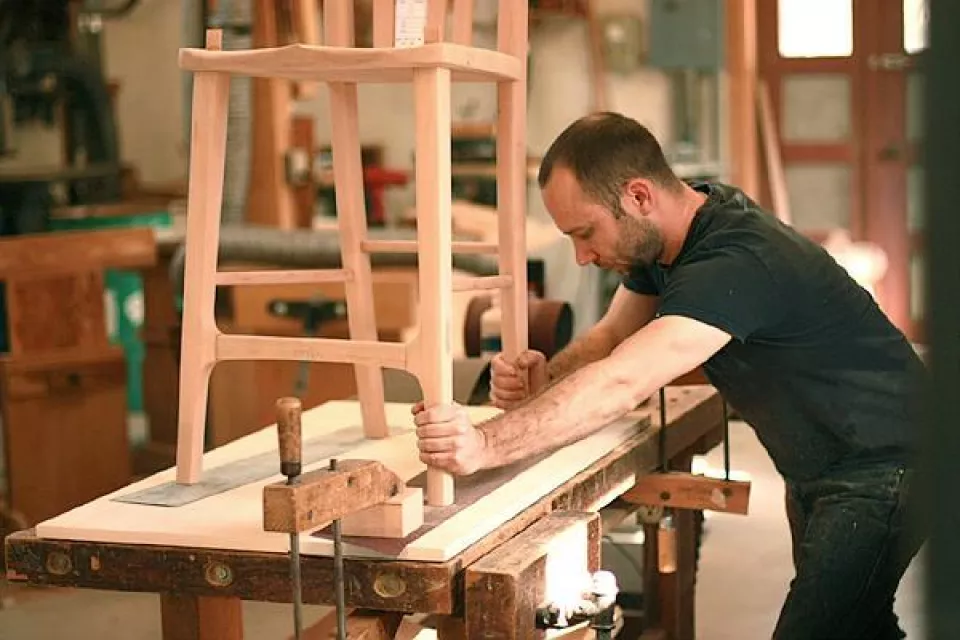
We bore the recess with the boring machine.
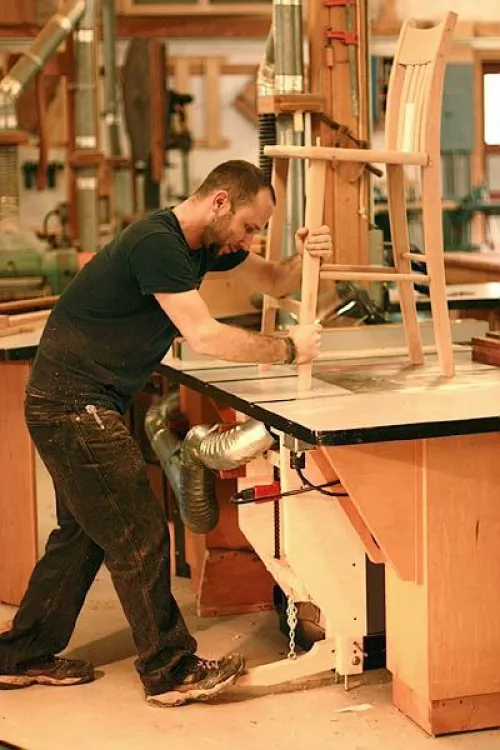
After finishing, we apply the pads. After many years—or much use, our chair-owners will likely need to replace felt. We’ll send new pads and these instructions: “Use pliers to pull out an old pad. Peel the backing off a new pad and stick it in the recess.”
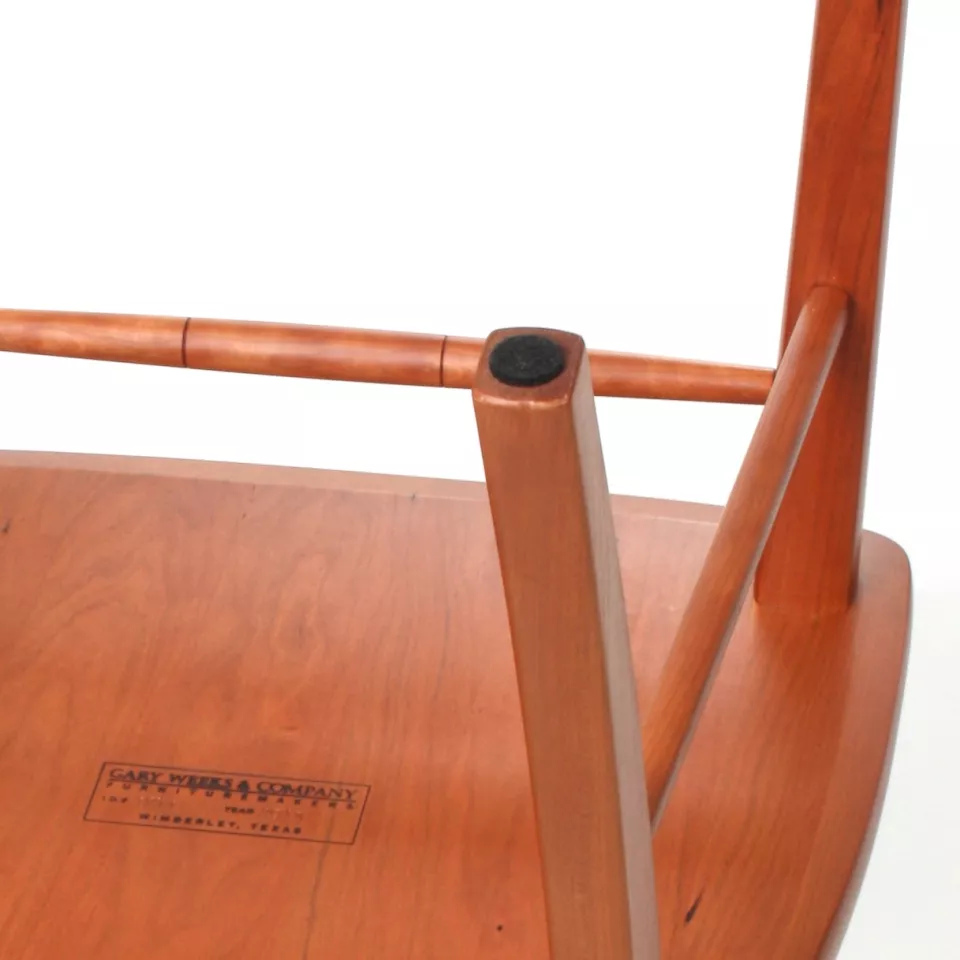