Stroke sanders were common in furniture factories and smaller shops until they were replaced, or better said, displaced by wide belt sanders. Our wide belt sander did not replace or displace our stroke sander. The wide belt sander made the stroke sander more efficient and effective. I hope to explain how.
Abrasives remove wood and leave scratches. The size and pattern of these scratches determines the quality of the surface: how it looks, how it feels, how it takes a finish. The smaller the scratches and the more even the pattern, the less visible, the smoother, and the more easily finished the wood. There is another quality of surface important to the eye, hand, and finish: fidelity to plane or contour. The fewer the ripples and waves, the better.
When I began work as a carpenter and cabinetmaker, the only belt sander I knew was a hand tool. It removed material quickly, especially if I did not hold that little platen flat, and usually left evidence of its use in ripples and waves in the surface. I found out about another kind of belt sander, a stroke sander, when I studied one on a visit to a church pew factory operated by a family friend. The principle was the same in the two machines, a belt ran over two pulleys and contacted the work under a platen. To use my belt sander, I held the pulleys, the platen, and the motor--the weight and its uneven distribution made it difficult to hold the platen flat. To use the stroke sander, the operator in the pew factory held the platen in one hand and moved the work back and forth beneath it with the other. The platen was light, balanced, and big enough to be stable on the surface. The moving table that supported the work was easy to glide back and forth. I could see what I was looking at.
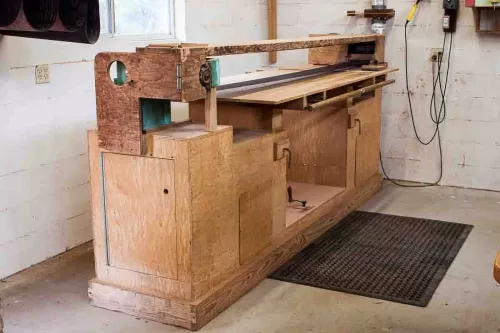
I bought the pulleys from an ad in the Fine Woodworking Magazine, threw away the given plans, and built the thing to a higher standard.
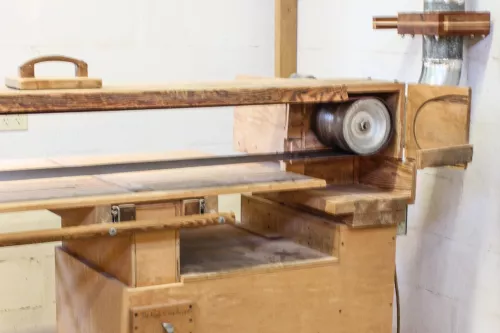
It immediately changed my shop life for the better and improved the surfaces that left the building.
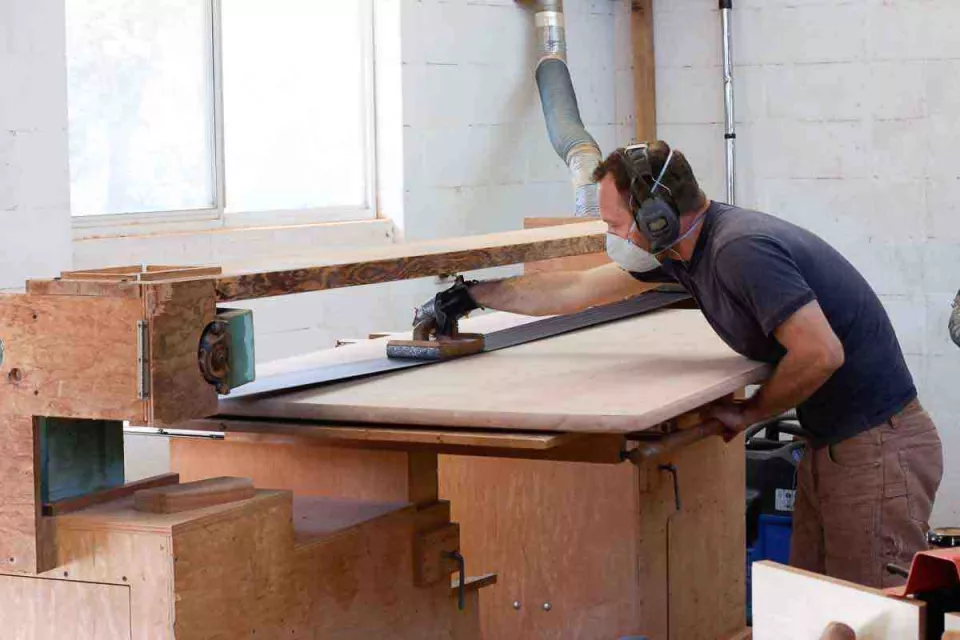