In June of 2008, we installed (finally) a compressed air system. We had a small job-site compressor to perform a few tasks, but it was completely inadequate to drive pneumatic sanders. We had built many, many pieces of furniture, and sculpted many chairs, with electric random orbit sanders, knowing that pneumatic sanders would save time — and wrists, but we were daunted by the cash investment and the time required to put an excellent, trouble-free (and moisture-free) “utility” in place.
This earlier post shows installing the compressor and addresses how important it has become.
At the original installation, we built a loop of 1″ iron pipe around the shop with drops to various stations and machines. Things change. We moved the pump sander and designed and built a pneumatic control valve for its dust ports, so we had to add a drop. Giving thanks for pipe unions and family heirloom cutters, threaders, and wrenches, Austin cut the main loop and added the drop. His grandfather and great-grandfather would be well pleased.
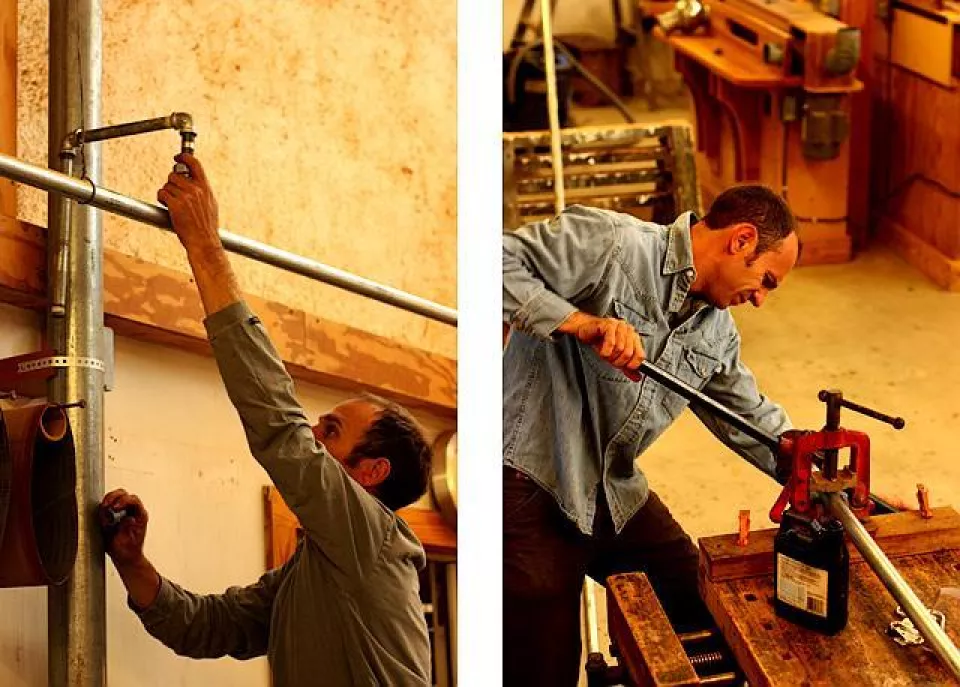
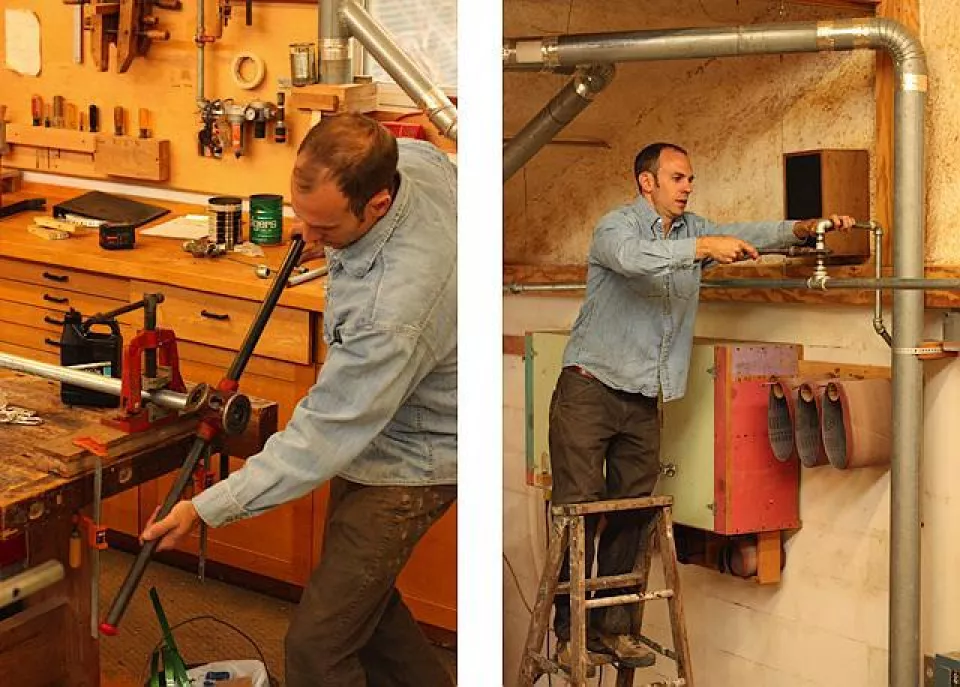